|
My brother gave me some chunks of lighter pine!


It is a fascinating wood, unique in it’s own way. Really heavy, since it is completely filled with resin.
I have no clue what to do with it. I am going to make a few handles out of a chunk just to see how it turns out. I wish I knew of a classic use apart from burning it.
Bob
Part 1, Part 2, Part 3, (Part 4,) Part 4.5, Part 5
I have had a chance to use the Grizzly Chisels now and have had a few updates in information. I decided that it was worthless to not trust my tools. So I went ahead and started to push my new Grizzly Japanese Chisel set. So far I have put and honed out three dings. That is not a lot considering that I have been working with osage and mesquite. Three dings is pretty low for seriously hard, tool eating wood. I have not been going easy on these tools. I have done a fair bit of work with several of them including the next smallest size and they have all held up fine. So I decided to go ahead and grind a point on the broken smallest one. The break was the one thing that gave me a few reservations about this tool set.
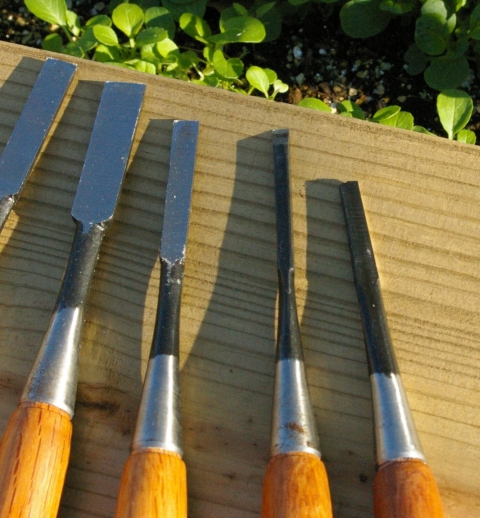
On close examination of the broken off tip and the remaining blade, I noticed that the black, ‘japanning,’ paint that covered the tool also covered part of the crack, where it was broken. In other words, it was cracked before they put the finish on the tool at the factory. Flaws like this happen, though we would rather they didn’t.
I called Grizzly’s support line and got to talk to Josh. Josh was quite helpful and understanding in this my time of need. Grizzly will be sending me a new chisel, so kudos to Grizzly, their tools and their support crew.
After I get the new chisel, I will clean it up, shape the handle and reset the hoop. Then I will put it through it’s paces. I will let you know the results in part 5, of this review.
Bob
Part 1, Part 2, Part 3, (Part 4,) Part 4.5, Part 5
The first thing I like to do, with a new gouge is make the sharpening tool for that gouge. I recently got a new set of gouges so I needed to make the gouge strop.

Michael Pilla, A good friend of mine from Philadelphia, sent me some delightful rock maple. Perfect stuff to make into a Gouge strop.
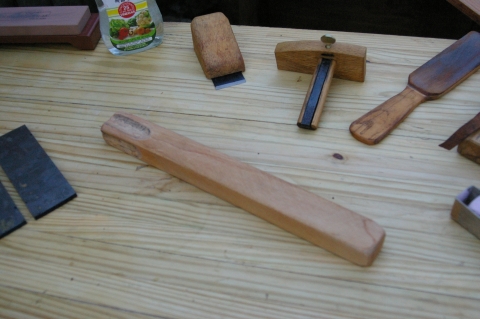
The chisel made the gouges in the gouge strop.
The a bit of oil and grit rubbed into the gouges, and I can strop the blades to decent enough sharpness.

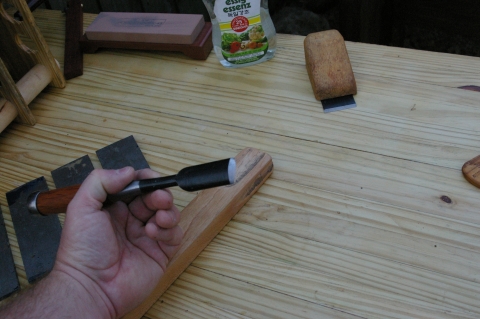
As you rotate the block you get a total of six grooves for tools to be sharpened in, one for each of the gouges.
x
x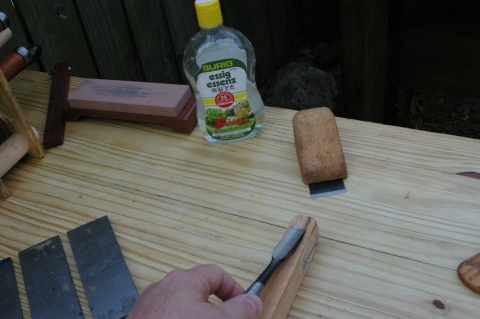
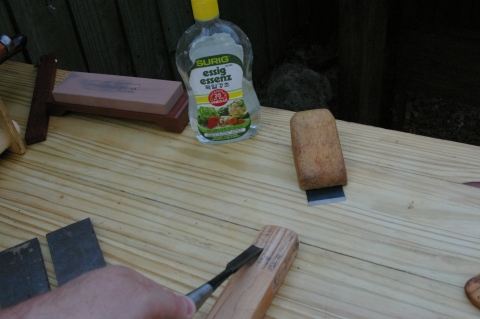
x x
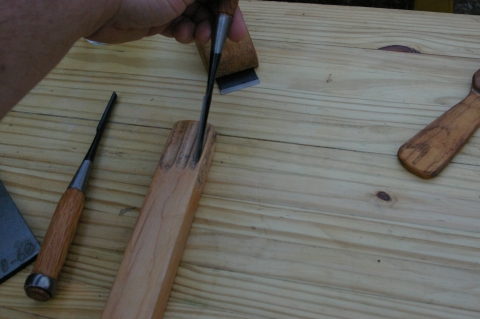
Here I am testing the gouge on pine endgrain. There is an nice example of smooth gouging of pine endgrain beneath my hand and in the vise.
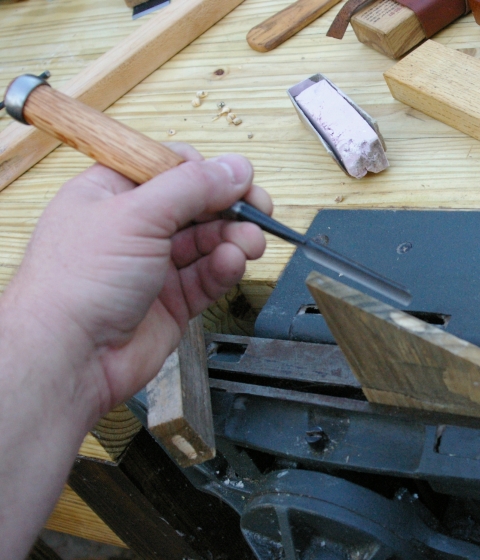
The best part about a gouge strop is that it seems to get better with time.
Bob
Lie-Nielsen had a Tool Event this last Friday, the 9th of January, 2009. I took the day off and my wife and I drove to Austin.
It was a very small show, but totally worth it. I got to see and touch all sorts of wonderful tools made by Lie-Nielsen! I also got to see the folk at Homestead Heritage. I would love to someday take a few classes from them, Paul Sellers made a very nice impression on me.
For me though, the real nifty was a little tool that John Economaki, from Bridge City Tools, demonstrated. The Jointmaker Pro is a pretty sweet tool. It does have a few limitations, for example it only cuts wood up to 6″ wide and 1-5/8″ thick. That being said, it is an amazing tool. It quietly, with astonishingly little mess, quickly makes perfect, easy to setup, smooth, precise finished cuts. It also does not have a plug.
I fell in love with the thing. I really, really want one! Did I mention that the first run of them will probably sell out, well before it ships? It is slated for shipping at the end of this month, so if I do get one, I probably won’t get it soon, since I will be close to the end of the line. It is however a rather big chunk of money for a fellow like me.
Another advantage is that the tool is going to be quite a bit safer than a power saw. No kickback or invisible spinning teeth. The teeth on the stationary blade are going to be frighteningly sharp, and could certainly hurt a person that did not work safely, but It will not kick up the same dust, throw things back at you, or slowly make you deaf. Since it is so much quieter, and cleaner, I will be able to stand, working it, while I watch movies with the wife and kids.
Fortunately my wife is a wonderful person. She can produce delightful meals inexpensively. If you have studied Indian or Korean foods, you can do amazing things with food at a very low cost. She treasures my safety and would like for me to spend more time watching movies with her and the kids. She just told me to call in the order. ^_^ We will be eating simple fare for a while.
🙂 I was a bit wicked when I ordered it. I asked if I could get one sooner, since I would blog and advertise it. Sadly these folk have integrity and operate on a first order get the first shipment basis. Very disappointing, hardly American really. OK, maybe far North American, but apart from folk like Lee Valley, you don’t see much of that these days. It gives me hope for our Nation.
Anyway, I will be using one to make things in a month or so, when it comes in. It will be fun to see what the new tool inspires me to make. I think some of my art may just go up a notch or two in quality. I may even work a bit faster.
Bob
Hand tool users online, often talk about the slope. It is a reference to the constant pressing need for new tools. It is really a fairly honest thing.
To start out making the simplest projects out of wood, you need to be able to cut wood and stick it together. A saw, hammer or screwdriver, and some glue will get you started. If you want to have smooth, splinter free wood most folk go for sandpaper. They should get a hand scraper and burnisher the same day they buy the sandpaper, but that requires a bit more knowledge.
As you add embellishments to your work, often a new tool will allow you to do the work better, in other words faster and prettier.
There is a point you reach, where the tools you need are fairly obscure or might not even exist commercially. This is not that historically rare. Custom tools at one time were the rule and not the exception.
Right now, for a few projects I am working on, I need a left handed skew plane. Normally this would not be a big issue since most people do their work in square. Since I am trying to do some fine work at 60 degree and 30 degree angles, there are times when I actually need, not just want, a left handed skew plane. Every other angled rabbet needs this tool. Without it you are forced to plane into the grain. This is the simple result of expanding your range of work.
I also want to make several sliding dovetails, and some nice grooves in wood for drawers to slide in. Since I am doing it at odd angles, the standard range of planes will not quite do. So I am designing a plow plane just for this task. The prototype has me optomistic.
As far as the tight set of tools that a woodworker might want in his travel tool box, these two might even make the cut. That makes them pretty important, by my standards.
Bob
|
|
Recent Comments