I am doing a bit of outdoor work and need a bit more of my wax mix, so I thought I would be kind and share the recipe and process.
The mix is very simple. Equal parts of Safflower Oil, Turpentine, and Paraffin.
For wax I am using a candle I bought cheap.
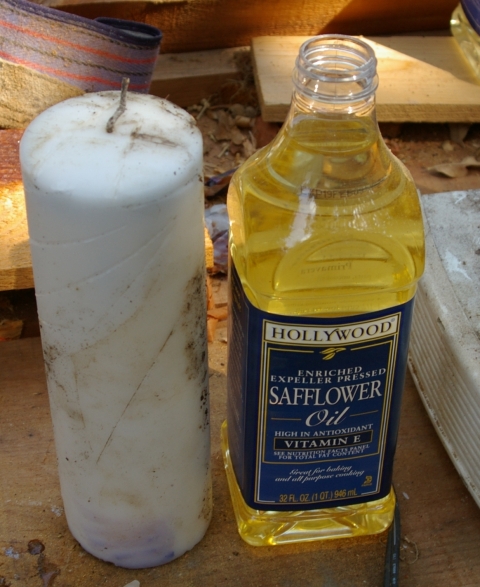
The candle is filthy, but instead of scraping off a layer of wax, I will skim the surface, let the dirt settle to the bottom of the molten wax, and filter it through a strainer. Because I am working outside while this stuff melts, I will probably have to remove leaves and sawdust anyway.

The wax is nearly molten here, and seems fairly clean so far. The can is a #10 bean can, and is in a small cheap sauce pan with a bit of water in it so the wax is in a double boiler. This limits the temperature to around the boiling temperature of water, and reduces the chance of the wax hitting critical temperature and bursting into massive flames. I am using an old electric hot plate, that has been through many an outdoor experiment.
After the wax is melted, I add the oil. This cools the wax and makes opaque white curdles. I wait till it is melted again before I add the turpentine. This again cools it. I wait until it is clear and put it in the odd tin or other containers I have collected for keeping wax in. I add the turpentine last as it is the most dangerous to put over heat. I am using an electric hot plate so that I don’t have open flames. I also have a wet towel ready in case anything happens.
This time, I added about two tablespoons of borax. Some of it won’t dissolve, but a bit of it will help preserve wood from mold, rot, insects and some corrosion, so it is good stuff to have.

I also decided to add some camphor. I mostly dissolved a block into the mix. Camphor repels some insects, and prevents some rust, so it may not be a bad thing to have the scent mixed into the tool handles.

To protect metal such as bandsaw blades and framesaw blades, I substitute food grade mineral oil instead of safflower in the same wax mix. Safflower oil thickens and eventually turns solid, so it will gum up on moving parts. Good for wood, bad for gears.
The safflower oil I use is High Linoleic Acid safflower oil. I use it instead of BLO for just about everything. is a superb drying oil and is used in quality oil paints. It does not tend to mildew or yellow. It dries slower, but you can instant dry it by heating it carefully over a burner. I treat wooden tools with the wax mix and quick cure the surface over a burner as well.
If the nutritional label has Polyunsaturated fat as a much higher number than Monounsaturated fat then it is the right stuff.

Note that the Polyunsaturated fat has a much higher number than Monounsaturated fat. The other safflower oil (High Oleic Acid) will have the opposite ratio. Before I use the oil, I test it. I open a bottle, and dab a bit on a scrap of paper, that I set under the bottle. I leave the bottle on the outdoor window sill of my workshop. It is out of the rain, but exposed to weather. If it thickens to a waxy resin in a couple of weeks, then I know it is the right stuff. I also leave the lid loose on the bottle. This allows it to breath. As a result it will dry faster when I do use it.
I get my safflower oil at my local Kroger’s Grocery.
A variation that I am also partial to is:
4 parts paraffin, 2 parts carnuba, 2 parts beeswax, 6 parts High Linoleic Acid Safflower Oil, 6 part pure gum turpentine, 1 part borax. These recipes are fairly classic.
Borax is the best of the best preservatives, but it tends to leach out. Waxing outdoor projects will slow leaching, Any borax you can get without leaving it gritty, that you can add to the paint and wax, is a good thing. If you don’t mind the grit, that might even be better.
Now for some background on safflower oil. Safflower oil history is a bit odd. Authoritative documents disagree regularly. Artists who have loved using safflower oil, change their mind and never use it again. It is considered drying, simi-drying and non drying. One person finds it to be the best for painting, another finds it to be useless.
Some sources will say it has been used in paint for 200 years, others will say 20. Carthamus tinctorius, safflower, has been cultivated by man since 1600 BC. It has been used as a dye for clothing, and makeup, and paint for ages.
The data on the use of the oil is pretty conflicting from where I sit. It started to be cultivated strongly in the U.S. about 1950. And has been used for paints ever since. A ‘mutation’ was discovered by the University of California, where the normal ratio of linoleic to oleic fatty acids is reversed. This gives a monounsaturated oil instead of polyunsaturated.
Drying oils are called drying oils because the will oxidize and otherwise harden. ‘Normal’ safflower oil is about 77% linoleic fatty acid, and 15% oleic fatty acid. Monounsaturated oils don’t dry. So the mutation does not dry well at all. The oil stays oily. Pure high linoleic acid safflower oil drys very well.
So if this is actually a reasonably common mutation, as mutations go, then it is likely that some people in the past have grown mixes, or reasonably pure strains one way or the other. As they selected the best producing plants to replant seeds from, they probably had no idea that the drying quality of the seed oil was being selected and altered as well. This would tend to make one artist love the stuff, but then abandon it later, and another artist hate it from the beginning. This would make a test fail or succeed at random.
I have had great success with safflower oil, yet I will be testing it for drying qualities before I use it. You never know when a farmer is going to save a different seed, or change seed suppliers. The old books on commercial soap making always advised you to test oils before making soap. Apparently oil adulteration and swapping has a very long history.
Another question is the long term reliability of oil as a finish. This is also an area, that well informed sources, give conflicting information. Humidity, temperature, pigments used, other chemicals, and environmental influences will all cause issues and make this a mixed area. Throw in the mistake, misidentification and the occasional authority making stuff up, and you end up with some very conflicting information. Now that a lot of fine oil paints are produced with safflower oil, and a lot of archival oils are based on safflower, there is a good chance that the curators of the future will be able to definitively give answers on safflower oil.

Above is the finished wax with a few tools soaking in it. The white spot on the surface is a bit of wax I put in to test temperature. Later when it cools, the mixture will harden into a nice thick paste.
Bob
Recent Comments